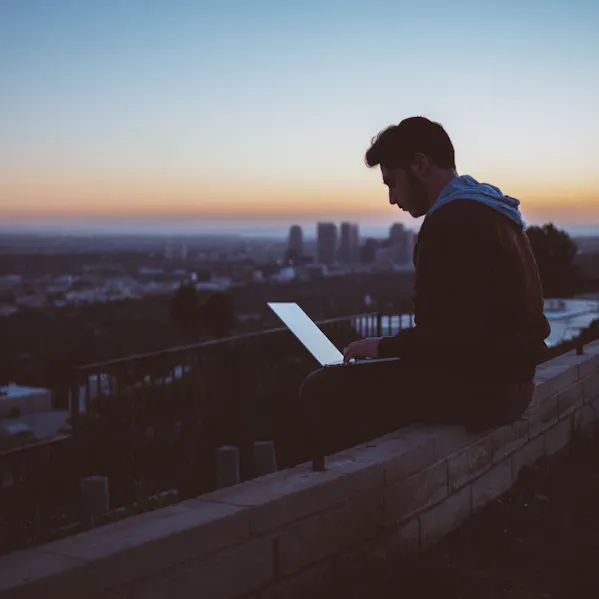
from the practice
CASE STUDY
AZO knows how a wide variety of demanding raw materials flow, trickle, mix and need to be stored. This is the core competence of the traditional company with over 70 years of experience. For years, the company has been developing from pure plant engineering to raw material automation for international customers.
This specialized knowledge means that no two plants are alike. This level of complexity makes documentation and maintenance of the plants as well as support by AZO employees a challenge.
Digital customer service and higher customer satisfaction. These were the resolutions of plant specialist AZO. No more individual, manual dispatch of technical documents, no more waiting times for customers. Thus, myAZOplus, the SAP-based customer portal based on SAP Commerce Cloud with 3D representation of the individual plant configuration, was created. Among other things, this allows technicians to identify and order spare parts at a glance.
What awaits you
The case study highlights the initial situation and describes the path to a digital customer and service portal with a digital twin, which enables customers to access individualized digital services such as plant documentation, e-learning modules, and spare parts identification.
With the help of All for One Customer Experience's own in-house developments, Equipmentviewer and Knowledge Management, the mapping and finding of plants and components is now possible on the basis of 3D models. For this purpose, the complete technical plant documentation with plant descriptions and drawings, brochures, certificates as well as a shopping cart for spare parts procurement has been integrated into the customer and service portal.
Request Case Study NOw!
THE EXPERTS FOR CUSTOMER EXPERIENCE
Within the All for One Group, All for One Customer Experience GmbH specializes in customer experience and solutions for sales, marketing, customer service and commerce. Learn more: